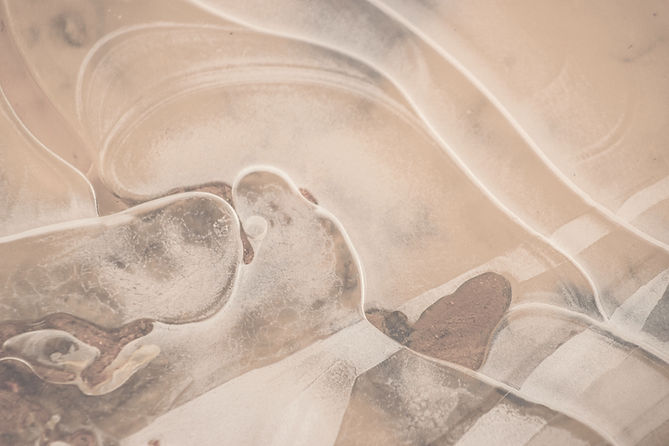
QUALITY
LEKOCH CUTLERY GOES THROUGH APPROXIMATELY 45 PROCESSES AND FINISHING TECHNIQUES, FOR EACH SINGLE PIECE

THE MANUFACTURING PROCESS
Production begins with a coil (reel) of stainless steel. The thickness of this coil should be the one of the final cutlery and the composition is as per the required quality. The first step is to cut the steel reel with a press (pressure: 100 to 150 T - fig 1.a.). This creates a blank, which is a coarse-shaped piece that can be used to produce several references (ex: table fork and spoon) of different patterns. It is referred to as multiple cutting. Several blanking dies will be used depending on the cutlery size (ex: table cutlery; dessert cutlery and fish cutlery; tea spoon and cake fork).
As shown on figure 1.a., the upper part of the blank is not wide enough to cut a spoon bowl. It will therefore need to be widened by being passed through a rolling mill (2 steel cylinders turning in opposite directions that will flatten the blank’s upper part). In order to obtain the requested width, two rolling mills will be used (fig. 1.b.).
The flattened blank will then be trimmed, i.e. the final outline will be cut with a press operating at 60-80T (fig. 1.c. and 1.d.).
THE MANUFACTURING PROCESS
For each item of each model, a different trimming die will be used (ex. Fig 2: Bercy tablespoon – ref 1690-2). The number of dies can be reduced while a same outline is used for several models (ex: Anser, Châtelet).
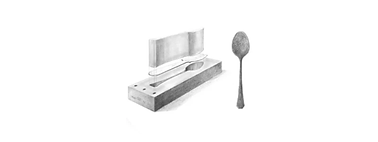

THE MANUFACTURING PROCESS
The pieces will then be stamped with a press that will give the final shape and ornamentation. The pressure will vary between 200 and 800 T depending on the size of the item and complexity of the decoration. Each item of each model requires a specific double die. Figure 4 features the stamping of a Contour tablespoon. Only the lower part of the die is shown.
More than 300 different dies will be necessary just for the Eternum Signature range, with more than 20 patterns.
THE MANUFACTURING PROCESS
This full process requires very accurate tools. Indeed, the different elements of the die must be perfectly adjusted and perfectly match the final result. The finishing of the stamping dies is fundamental. The ornamentation of the pattern must be perfectly engraved. Figure 5 shows some of the tools used: silversmith’s hammer, stylus, milling cutters, etc.


THE MANUFACTURING PROCESS
Once stamped, the cutlery still needs to be polished. The first step is the polishing of the edges, which are made perfectly smooth by being passed along 3 abrasive belts with a more and more finer grain. The operating machines (picture 7) are regulated in such a way that the grinding belts accurately follow the cutlery outline.
THE MANUFACTURING PROCESS
The final polishing of the edges is realized thanks to the experience and know-how of the manual polishers (picture 8). They will make the matt or brilliant finish depending on the pattern.
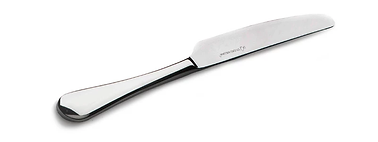
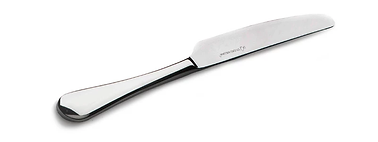
THE MANUFACTURING PROCESS
The second step is to polish the cutlery’s back and front. This is a fully automated process involving a series of polishing machines (picture 9). Each machine is set to perform a specific operation. 7 machines are needed to polish a spoon.
Once out of the last machine, the pieces of cutlery are placed one by one (so that they are not damaged) in a degreasing machine for cleaning. They will then be controlled, and automatically packed in plastic bags: 12 pieces per box ready for delivery.
SPECIAL STEPS FOR THE KNIVES
There are two types of knives:
The monobloc knives: these are made up of one piece of steel and usually used with low-cost or middle-cost cutlery.
The hollow handle knives: the blade and handle are soldered together and the steel is usually a 18/8 or 18/10 steel.
For knives, the steel is heated and then tempered to ensure the solidity of the blade and to guarantee an effective and long-lasting cutting edge. All our knives have a 48 Rockwell hardness minimum that guarantees their quality.
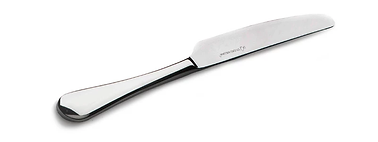